Saving Energy Step 3 ? Towards a Variable Energy Bill
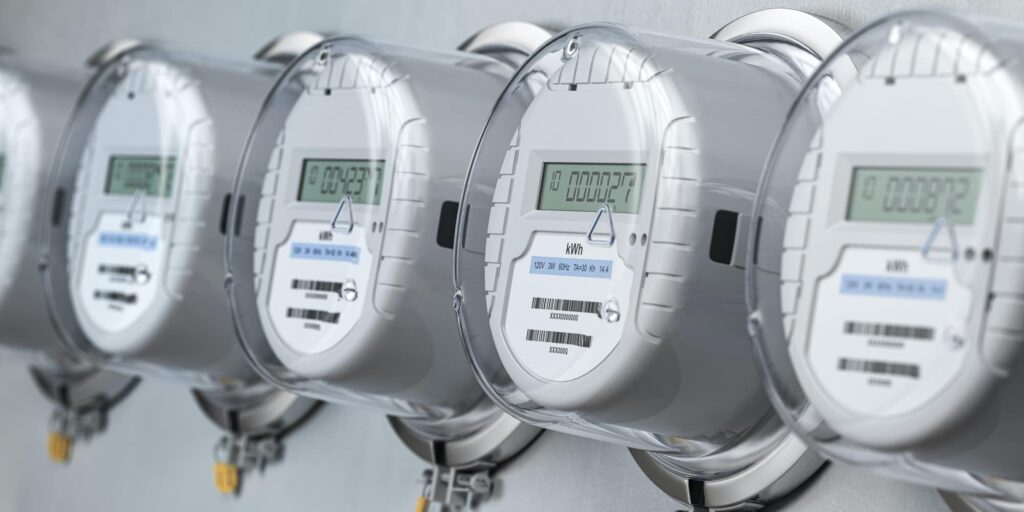
Do you remember the days when energy was so cheap we paid the bill almost without thinking about it? Things have changed and we have the additional duty of reducing consumption to help save the planet. This is the third article in our mini-series on saving energy. It follows on from the first that explored […]
What ISO 14001 Status did for Cummins Inc.
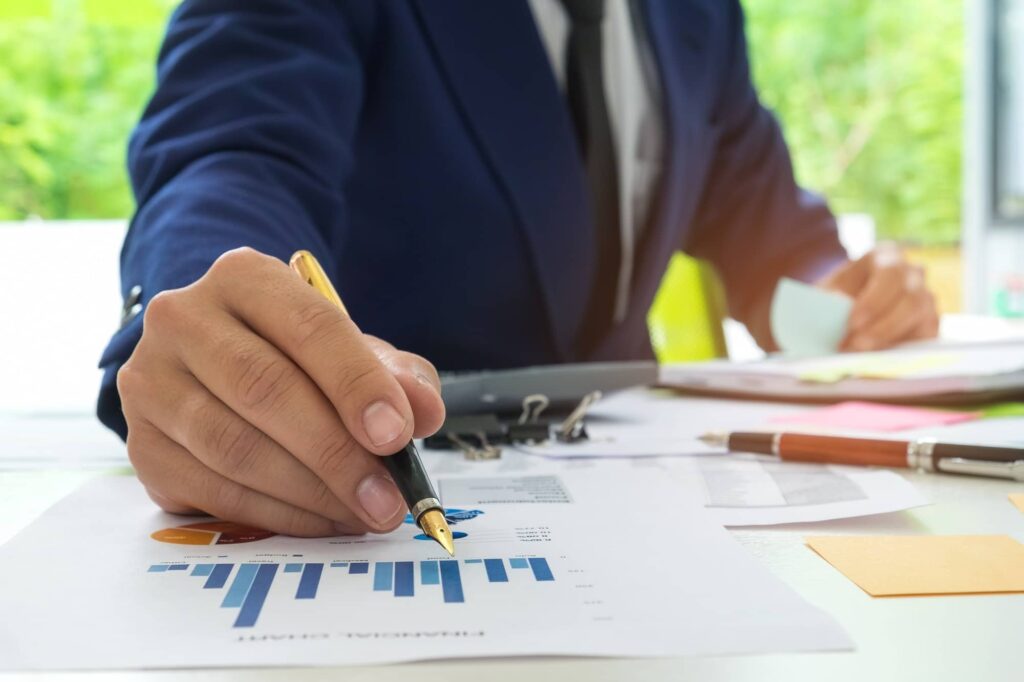
Cummins manufactures engines and power generation products, and has been a household name almost since inception in 1919. It sells its products in over 300 countries, through approximately 6,000 dealerships employing 40,000 people. Because its product line runs off fossil fuel it is under steady pressure to display a cleaner carbon footprint. Cummins decided to […]
When Carrefour Pushed the Right Buttons
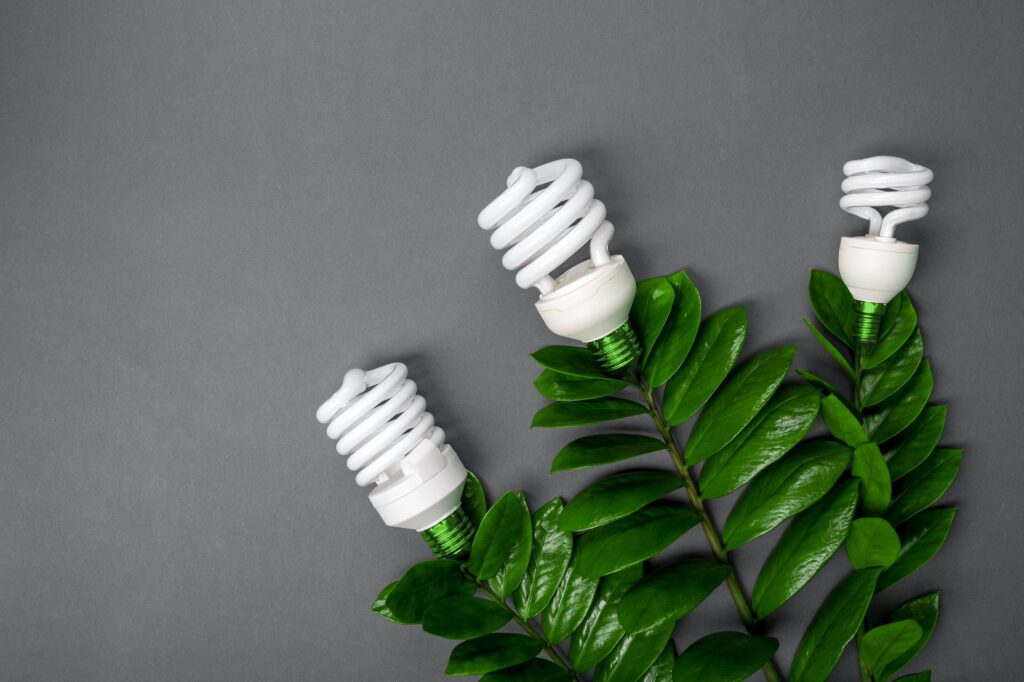
Retail giant Carrefour based in Boulogne Billancourt, France is big business in anybody?s numbers. Europe?s #1 retailer opened its first store in 1958 near a crossroads (Carrefour means ?crossroad? in French) and has largely not looked back since then. The slogan for the hypermarket chain with more than 1,500 outlets and close to a half […]
Symbion Pharmacy Services? Definition of Responsibility
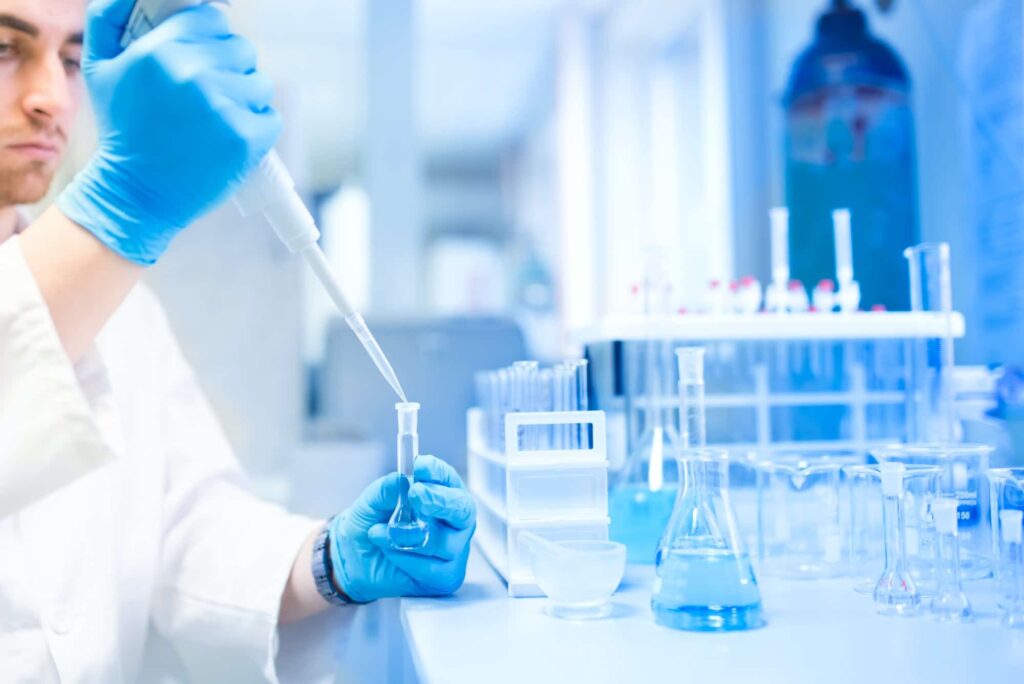
A ?symbion? is an organism in a symbiotic (i.e. mutually beneficial) relationship with another one. In the case of Australia?s giant Symbion Pharmacy Services, this means supplying and delivering over-counter Chemmart medicines to more than 3,000 hospital and retail pharmacies, while remaining mindful of its carbon footprint. In 1999, the company with the tagline ?life […]
How Accenture Keeps Rolling Out Sustainability
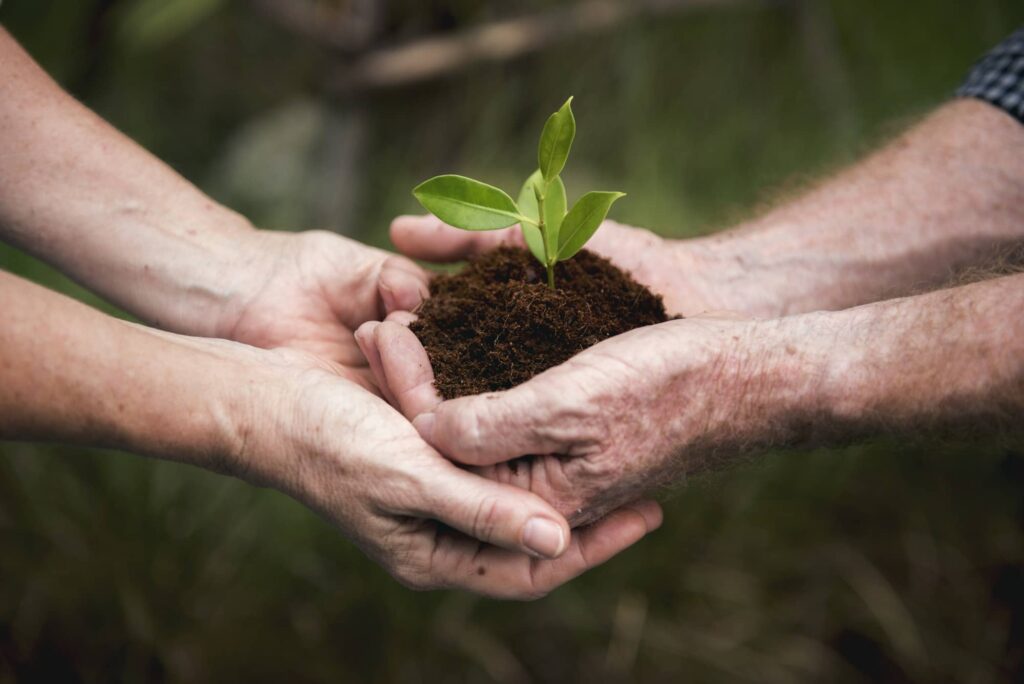
Multinational management-consulting and technology-services company Accenture has a good eye for sniffing out new business, with 305,000 employees advancing its interests in more than 200 cities in 56 countries evidence. Last year, it netted US$30 billion profit that is a tidy sum of money in anybody?s books. Accenture also practices what it preaches. This is […]
What Energy Management Software did for CDC

Chrome Deposit Corporation ? that’s CDC for short ? reconditions giant rollers used to finish steel and aluminium sheets in Portage, Indiana by applying grinding, texturing and plating methods. While management was initially surprised when the University of Delaware singled their plant out for energy assessment, this took them on a journey to bring energy […]
How Mid-South Metallurgical cut Energy Use by 22%
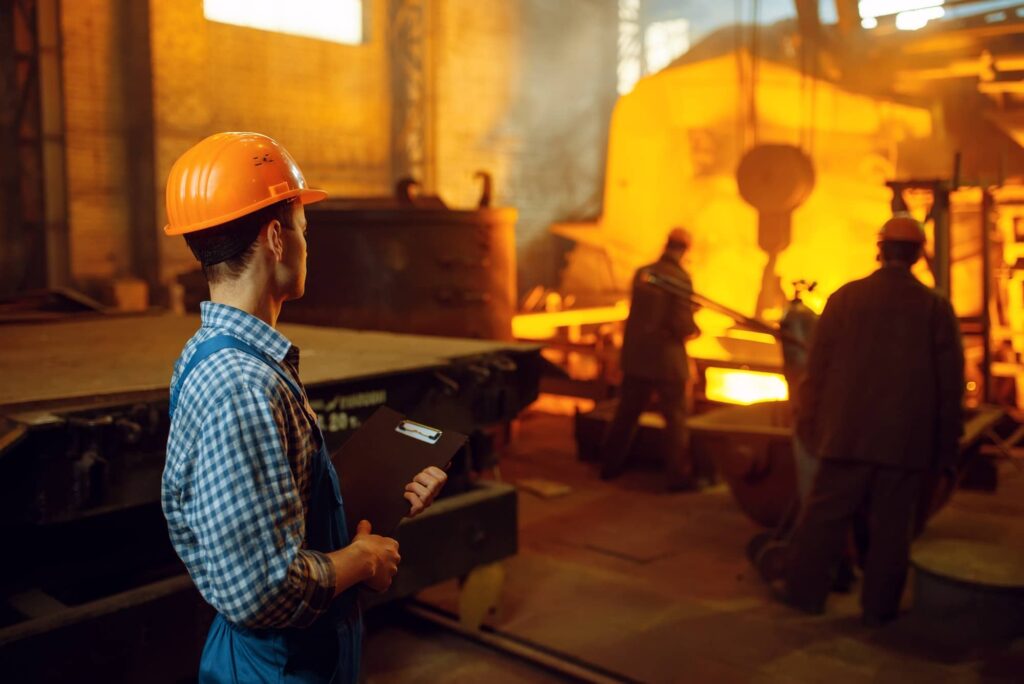
Mid-South in Murfreesboro, Tennessee operates a high-energy plant providing precision heat treatments for high-speed tools – and also metal annealing and straightening services. This was a great business to be in before the energy crisis struck. That was about the same time the 2009 recession arrived. In no time at all the market was down […]
How Alcoa Canned the Cost of Recycling
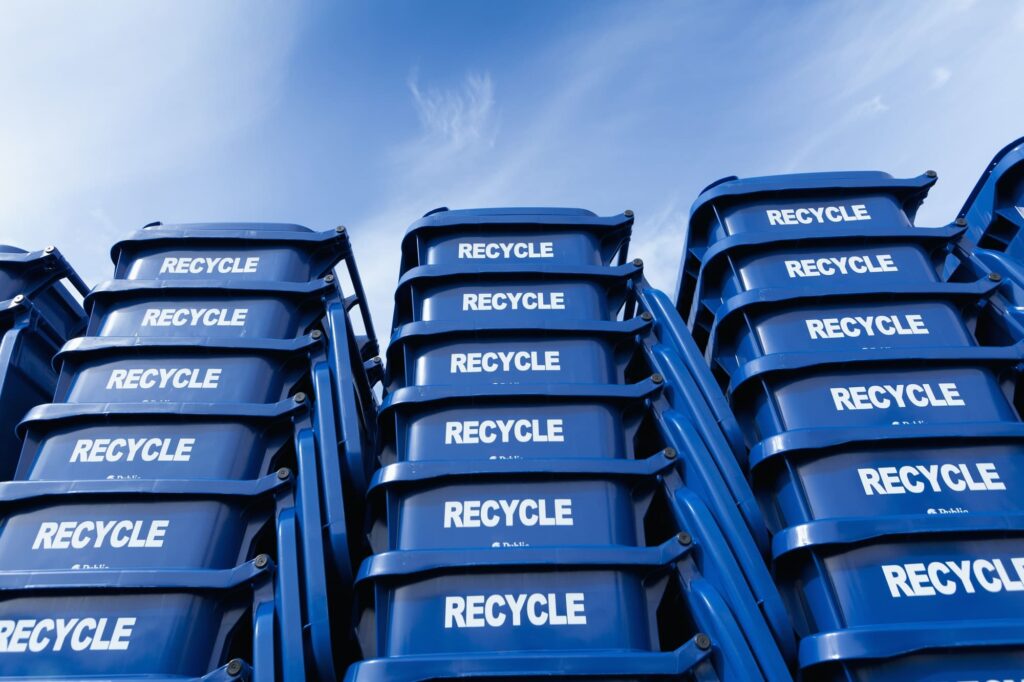
Alcoa is one of the world?s largest aluminium smelting and casting multinationals, and involves itself in everything from tin cans, to jet engines to single-forged hulls for combat vehicles. Energy costs represent 26% of the company?s total refining costs, while electricity contributes 27% of primary production outlays. Its Barberton Ohio plant shaved 30% off both […]
FUJIFILM Cracks the Energy Code
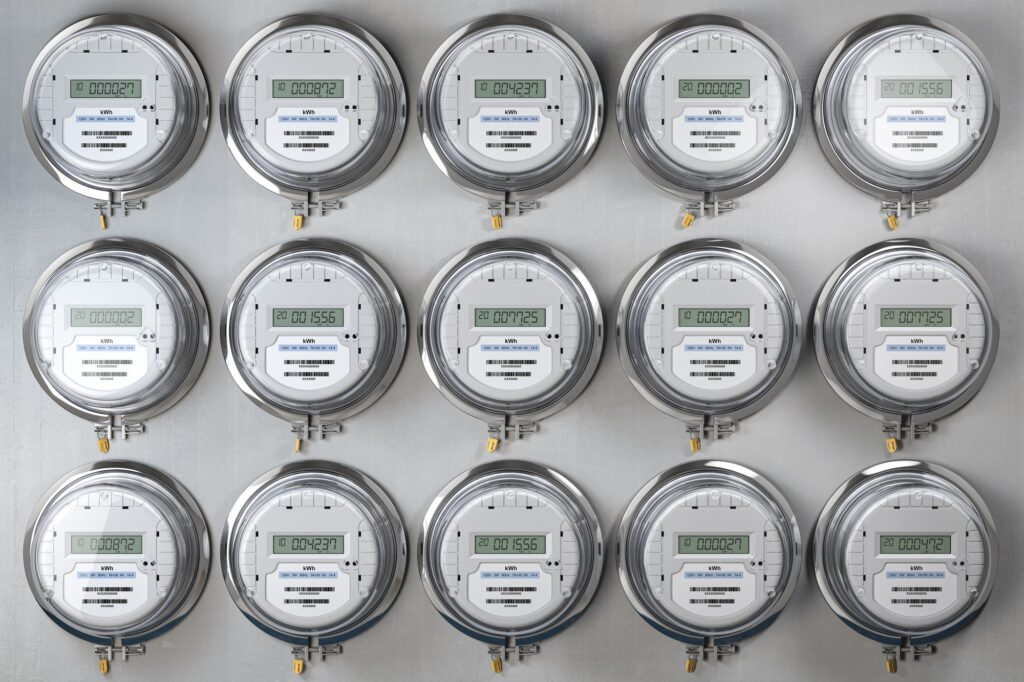
FUJIFILM was in trouble at its Dayton, Tennessee plant in 2008 where it produced a variety of speciality chemicals for industrial use. Compressed-air breakdowns were having knock-on effects. The company decided it was time to measure what was happening and solve the problem. It hoped to improve reliability, cut down maintenance, and eliminate relying on […]
Energy Savings Opportunity Scheme (ESOS): An Overview
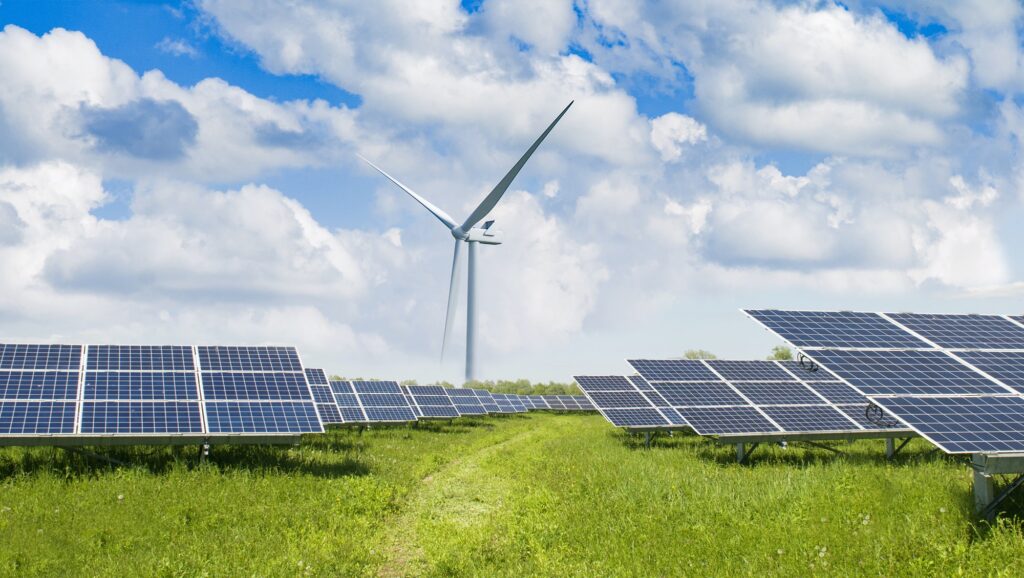
Energy management is crucial to most businesses in the UK. This is primarily because energy usage substantially affects all organizations, whether large or small. The good news is that, energy costs can be controlled through improved energy efficiency. And this is exactly why Energy Savings Opportunity Scheme (ESOS) came into being ? to promote competitiveness […]